In the realm of construction projects, finding ways to maximise space utilisation is paramount. One remarkable solution that has proven to be a game-changer is incorporating mezzanine floors. A mezzanine floor is a type of intermediate level situated between the main floors of a building, providing an additional platform for various purposes.
Mezzanine floors have an array of applications across diverse industries. From expanding storage capacity in warehouses to creating extra office space in commercial settings and optimising workflow in manufacturing facilities, these versatile structures have become a go-to solution for space optimisation.
Here we will delve into the world of mezzanine floors, exploring their definition, usage in construction, and the wide-ranging benefits they bring. Join us as we uncover the transformative power of mezzanine floors and how they revolutionise how we optimise space in construction projects.
Understanding Mezzanines
Mezzanines, in the context of construction, refer to intermediate floors inserted between the primary levels of a building. These additional platforms effectively utilise vertical space, transforming underutilised overhead areas into functional and productive spaces.
The primary purpose of mezzanines is to maximise space utilisation, allowing businesses and organisations to expand their operations without the need for costly building extensions or relocations.
Mezzanines find applications across various industries, including warehousing, retail, commercial spaces, and manufacturing facilities. They offer a flexible and efficient solution for adding storage, creating additional office areas, accommodating machinery, or optimising workflow.
Types of Mezzanine Floors
We will discuss this from two perspectives: Types of mezzanine floors based on materials and types of mezzanine floors based on applications.
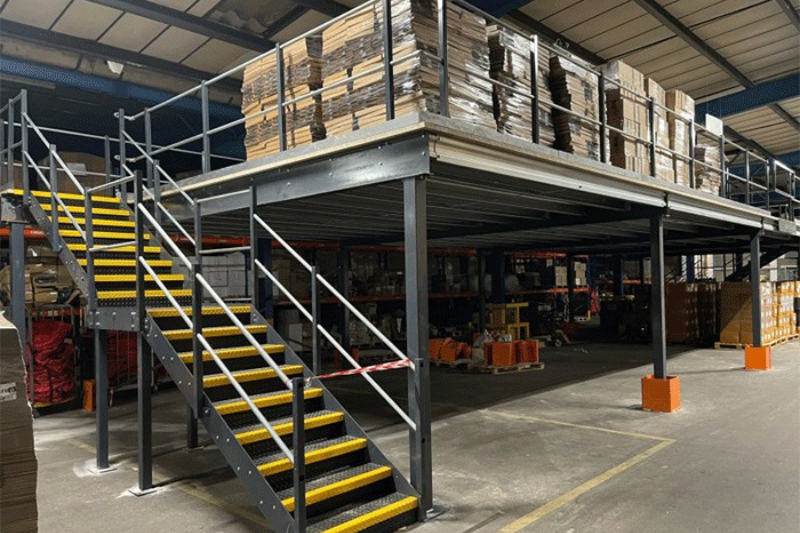
Types of mezzanine floors based on applications
Mezzanine flooring is widely used in various industries and spaces to optimise available space and cater to specific needs. Whether it's in industrial sites, warehouses, offices, or retail establishments, mezzanine floors offer valuable solutions for expanding usable areas. Here are the varying types of mezzanine floors based on their usage:
Warehouse mezzanine floor
One of the most common applications of mezzanine floors is in warehouses and storage facilities. Warehouse mezzanines provide additional space for packaging, sorting, and storing goods, making it easier to organise inventory and improving operational efficiency.
Industrial mezzanine floor
Industrial settings often utilise mezzanine floors as work platforms. Industrial mezzanine floors offer elevated spaces for machinery installations, production lines, or assembly work, optimising workflow and providing a safe and efficient work space.
Retail mezzanine floor
In the retail industry, mezzanine floors are used to create additional selling space or display areas. Retail mezzanines enable businesses to maximise their floor area, allowing for the expansion of product lines, creating customer seating areas, or establishing elevated showcases.
Office mezzanine floor
Mezzanine floors are also employed to create office spaces within larger facilities. In commercial buildings or industrial complexes, office mezzanines provide dedicated spaces for administrative work, meetings, or collaborative activities, allowing businesses to utilise available vertical space efficiently.
Workshop mezzanine floor
Workshops often require specific areas for specialised tasks or equipment. Mezzanine floors can be customised to accommodate workshop needs, providing designated spaces for woodworking, metalworking, or other craft activities. Workshop mezzanines ensure efficient space utilisation while keeping work areas separate and organised.
Portable mezzanine floor
Portable mezzanine floors are versatile and movable structures that can be assembled and disassembled. These temporary mezzanines are ideal for trade shows, events, or projects that require flexible and adaptable space solutions.
Types of mezzanine floors based on materials
Regarding mezzanine floors, several types are available, each designed for specific purposes and constructed using different materials. Whether you need a sizable structural system or a small storage platform, understanding the different types of mezzanine floors can help you choose the right one for your needs. Here's an overview of the main types of mezzanine floors:
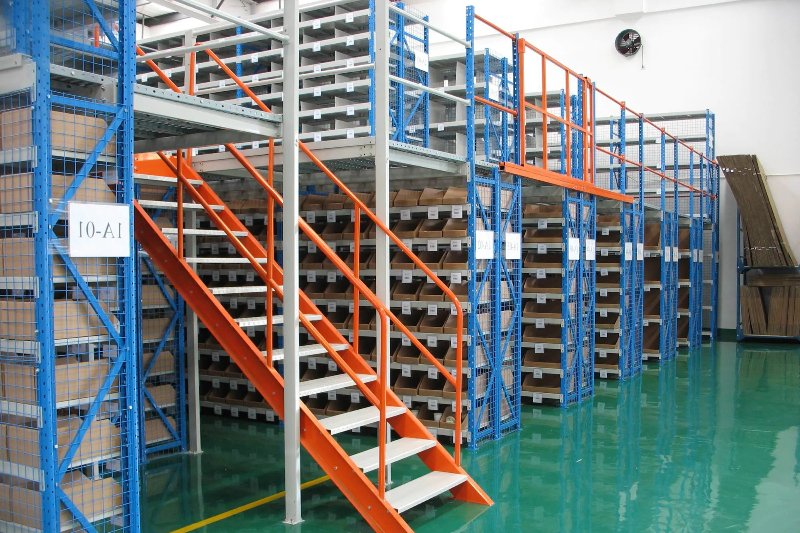
Steel mezzanine floor
Steel mezzanine floors are commonly used in industrial settings. They are made from high-strength steel, providing excellent durability and load-bearing capacity. Steel mezzanines offer a versatile solution for creating additional workspace, storage areas, or equipment platforms within a facility.
Rack mezzanine floor
Rack-supported mezzanine floors are integrated with existing racking systems. The mezzanine floor is constructed on top of the racks, utilising the vertical space between the floor and ceiling. This type of mezzanine floor is great for maximising storage capacity while maintaining easy access to stored items.
Concrete mezzanine floor
Concrete mezzanine floors are constructed using reinforced concrete slabs. They offer high strength and durability, making them suitable for heavy-duty applications. Concrete mezzanines are commonly used in industrial environments requiring robust floorings, such as manufacturing plants or warehouses.
Bar grating mezzanine floor
Bar grating mezzanine floors feature an open-grid design made of steel bars. This design allows for airflow, light penetration, and easy drainage. Bar grating floors are commonly used in environments with essential ventilation or drainage, such as wet areas or facilities that handle liquids.
Wooden mezzanine floor
Wooden mezzanine floors are often used in commercial or office spaces. They offer a more aesthetically pleasing option and can be designed to match the existing interior decor. Wooden mezzanines are lightweight and easy to install, making them popular for creating additional office spaces, showrooms, or retail areas.
Mezzanine Floor Construction and Installation
Here is a guide on how to design and construct mezzanines:
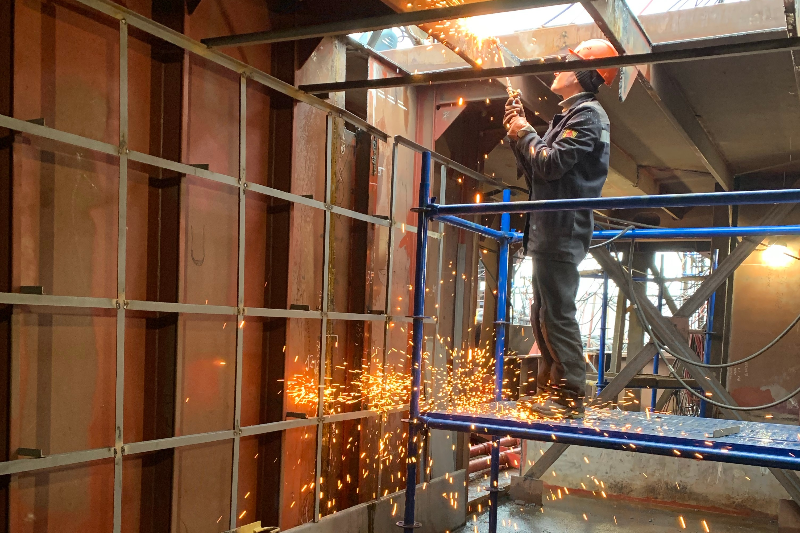
Step One: Design considerations
When designing mezzanines, pay attention to the following:
Load-bearing capacity
Before constructing a mezzanine, assessing the load-bearing capacity of the existing building structure is essential. This evaluation ensures that the building can support the additional weight of the mezzanine, including its occupants, equipment, and storage items.
Consulting with a structural engineer is highly recommended to accurately determine the maximum load capacity and verify the feasibility of installing a mezzanine.
Building codes and permits
Compliance with local building codes and regulations is crucial when planning and constructing a mezzanine. Building codes vary by jurisdiction but typically cover aspects such as structural integrity, fire safety, accessibility, and emergency exits. It is imperative to obtain the required permits and approvals from the relevant authorities before proceeding with the construction process.
Step Two: Construction process
After designing, the next stage is construction, which involves the following:
Structural elements
Mezzanines consist of several key structural elements that ensure their stability and durability. These include:
- Beams: Horizontal load-bearing members that support the floor and distribute the weight to the columns or walls.
- Columns: Vertical supports that provide stability and bear the weight of the mezzanine.
- Decking: The surface of the mezzanine floor, which can be constructed using numerous materials such as steel, wood, or composite panels.
- Guardrails: Safety barriers that prevent falls from the edges of the mezzanine, typically constructed using handrails and kick plates.
The selection of appropriate materials for these structural elements depends on factors such as load requirements, fire resistance, aesthetics, and maintenance considerations.
Step Three: Installation and assembly
The mezzanine installation typically involves the following steps:
Site preparation
Clearing the designated area and ensuring it is level and free from obstructions.
Framework assembly
Erecting the columns, beams, and other supporting structural components according to the design specifications.
Flooring installation
Placing and securing the chosen decking material to create the mezzanine floor.
Guardrail installation
Installing the guardrails along the edges of the mezzanine to ensure safety.
Integration with services
If necessary, integrating utilities such as lighting, HVAC, electrical wiring, and fire suppression systems into the mezzanine structure.
Safety measures
Implementing safety measures, like signage, emergency exits, and proper lighting, to comply with building codes and enhance occupant safety.
Note: Professional installation by experienced contractors or construction teams is highly recommended to ensure the mezzanine is structurally sound, complies with regulations, and meets safety standards.
Applications of Mezzanines in Construction
Mezzanines offer versatile solutions for optimising space and enhancing functionality in the construction industry. Here are some critical applications of mezzanines:
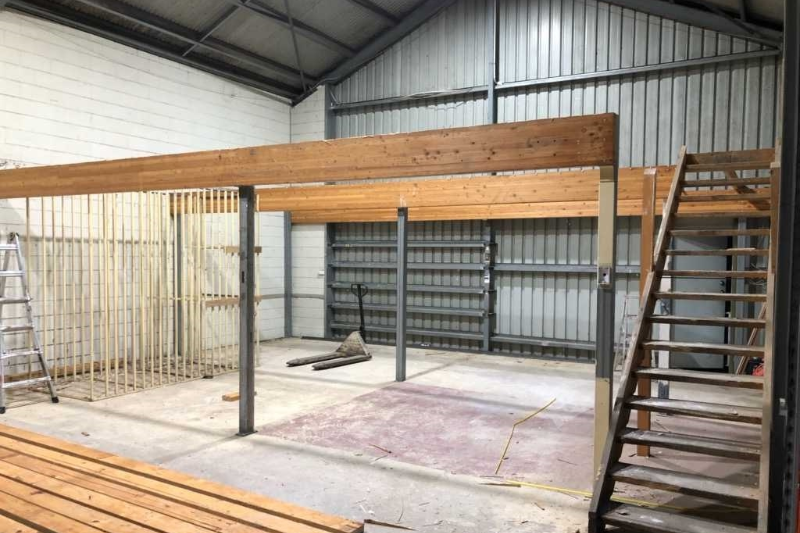
Additional workspace
Mezzanines create extra office space, workstations, or meeting rooms without extensive renovations, ideal for businesses experiencing growth or maximising available square footage.
Storage and inventory management
Mezzanines efficiently utilise vertical space, providing extra storage for goods, equipment, and inventory in warehouses and distribution centres.
Equipment and machinery platforms
Mezzanines accommodate heavy machinery and production lines, optimising floor space and workflow in manufacturing and industrial facilities.
Retail and showroom areas
Mezzanines expand retail and showroom space, offering additional display areas, product showcases, and customer seating to enhance the customer experience.
Construction site offices
Mezzanines serve as temporary offices or management areas during construction projects, providing designated spaces for project managers, engineers, and administrative staff.
Observation decks and viewing platforms
Mezzanines offer elevated areas for stakeholders, visitors, and the public to observe and appreciate the progress of large-scale construction projects.
Maintenance and service access
Mezzanines provide convenient access to building maintenance areas, such as HVAC systems or electrical panels, ensuring separation from common workspace areas. Mezzanines revolutionise construction by providing versatile solutions for various needs, enhancing productivity, and maximising space utilisation.
Consult a Mezzanine Expert Today
Incorporating a mezzanine into your construction project can revolutionise space utilisation and enhance efficiency. Mezzanines offer a practical and cost-effective solution for expanding operations without expensive renovations. Mezzanines provide flexibility and adaptability if you need extra storage space, a larger retail area, or an optimised workflow.
Collaborate with experts in custom mezzanine design and construction to unlock the full potential of your available space. It is the fastest way to take your business to new heights through optimised space utilisation and success.